The Environment
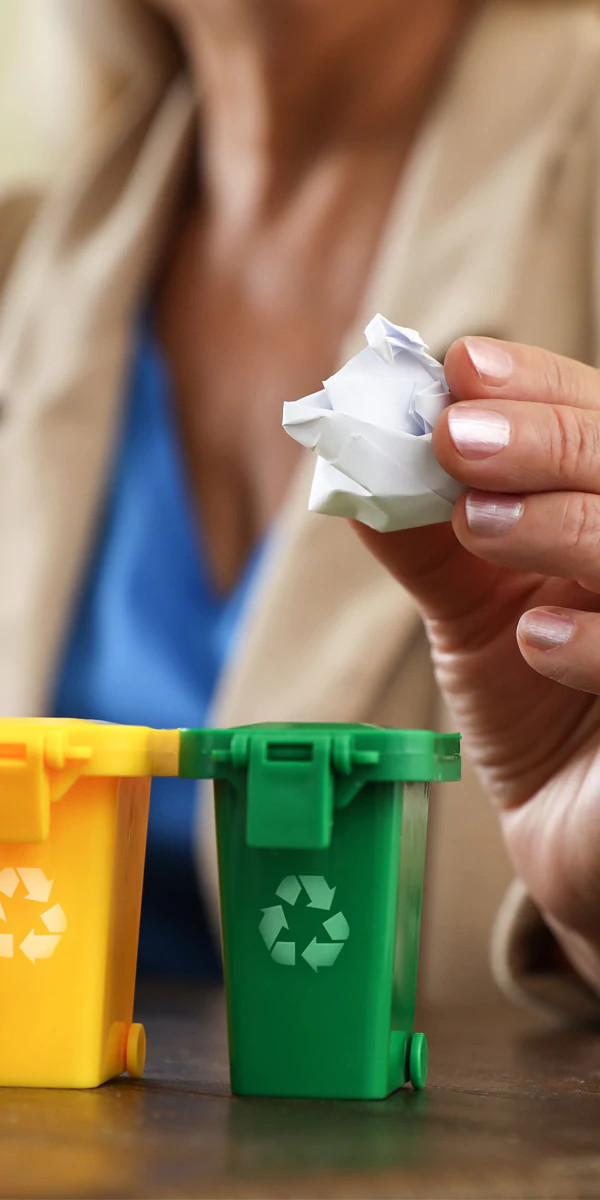
Overview
The Group’s decisions and activities have an impact on the environment. The impacts arise from the Group’s use of resources, location of the Group’s activities – whether in rural or urban areas, the generation of pollution and waste, and the impact of the Group’s activities on the broader environment.
To reduce its environmental impacts, the Group adopted an integrated approach that takes into consideration the direct and indirect economic, social, health and environmental implications of its decisions and activities.
Management Approach
Environmental stewardship is a key responsibility of our management, which carries both financial and physical risks. The Group ensures that its operations comply with environmental laws, voluntary and international best practices and standards to avoid, minimise and mitigate negative impacts on the environment. Through accurate reporting, our performance as well as the performance of others within our sphere of influence can be improved. The Group calculates its carbon footprint in order to understand its current impact on climate change, allowing it to establish and to optimise the Group’s use of resources while minimising its environmental impacts and reducing long term risks.
Scope of Data
Sustainability reporting is a continuous improvement process where we aim to expand the scope that’s being reported on gradually over time at the same time as ensuring the data we collect is accurate. It is a continuous process of improving efficiency through accurate data collection and over the course of the reporting year, the Group has incorporated more precise data and information collection from an environmental perspective through its quarterly sustainability reporting and analysis initiatives.
In F2024 the Group started to collect owned fleet data as well as progressing towards collecting third party fleet data. To ensure the accuracy of the fleet data reported in this report, the Group will incorporate this data from F2025 onwards.
This financial year the animal rearing businesses focused on recording only the solid waste produced by their operations. Manure as organic fertiliser used on pastures is therefore no longer included in the total waste produced by the Group. However, it continues to benefit the Group’s farms’ pastures as well as those of local farmers in the vicinity.
Waste Management
The Group abides by the zero waste to landfill philosophy by committing to the 4 R’s (Reduce, Re-use, Recycle and Recover) and Best Environmental Option (BEO) management systems.
Management Approach
The Group recognises the significant environmental impacts of production waste and end-user, post-consumer waste generated through our operations and products. This includes solid waste, hazardous waste, effluent and air emissions. The Group strives to optimise operational efficiency to minimise waste and the potential for pollution is evaluated, measured, monitored and managed through Group policies, site inspections of waste generating points to ensure they are within stipulated specifications.
In particular, the Group’s standard operating procedures on waste management are guided by the Environmental Management Act (20:27), Section 60 and the Environmental Management (Effluent and Solid Waste Disposal) Regulations, Statutory Instrument number 6 of 2007, SI72/2009 and City bylaws for effluent disposal.
During F2024, the Group produced a total of 14 003 tonnes of waste, and following the Group’s commitment to the 4Rs, 10.73% of the waste was disposed at landfills.
The Group’s types of waste are presented in the chart below:
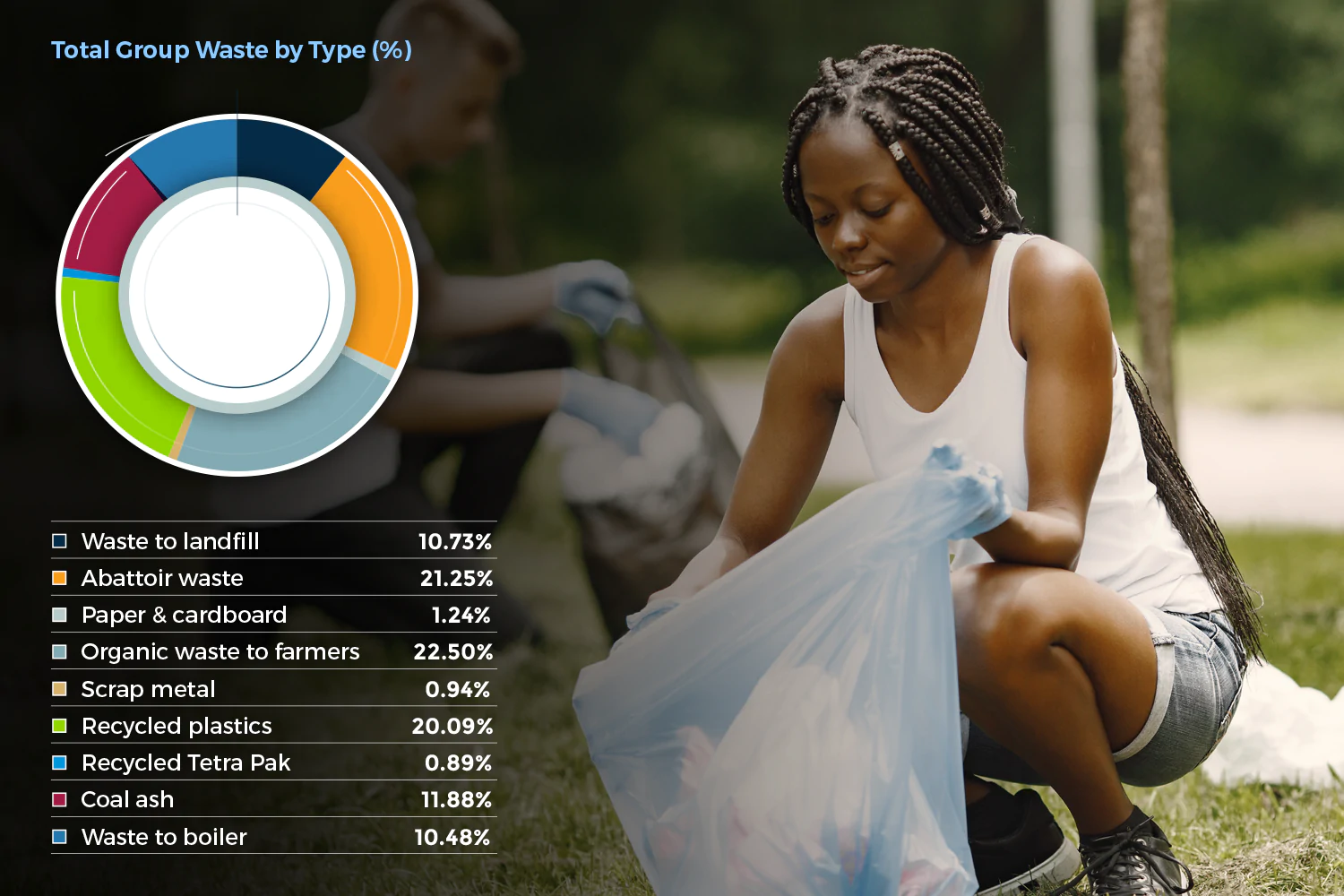
Recycled Waste
The Group implemented alternative disposal methods for 89.27% of its waste, therefore minimising the volume ending up on landfill. 20% of the Group’s waste was plastics, 1.24% paper or cardboard waste and 0.94% scrap metals. By working with third parties, these items of recyclable waste were collected and became the raw materials for local enterprises. For example, 100% of TBBC's PET plastic waste was recycled by being converted into straps used by brick moulders while recycled plastic from Prodariy was made into pellets and irrigation pipes. Coal ash from the coal boilers equating to 11.88% of the Group’s waste were sold to local brick makers. During the reporting year 1 467 tonnes of waste was incinerated in the National Foods’ two cyclonic boilers reducing its reliance on coal and reducing the volume of waste to landfill.
A number of businesses produce waste which is suitable as livestock feed, e.g. wasted milk and juice, maize screening and masese from the brewing process. 3 151 tonnes were sent to farmers in F2024 equating to 22.50% of the volume of waste produced by the Group.
In F2024 Prodairy was one of the signatory to the newly formed Zimbabwean Pact for Carton Recycling whose purpose is to provide an end-to-end recycling solution and create a circular economy for carton packaging in Zimbabwe. The Pact brings together stakeholders, including Zimbabwean brand owners such as Prodairy, Dairiboard, Kefalos, Montgomery, Dendairy, the Dairy Processors Association of Zimbabwe, as well as waste management operators. Working together with Tetra Pak, the initial phase of implementing the Pact is to focus on developing a collection infrastructure and value chain for used carton packaging to be exported to South Africa’s paper mills for recycling. Prodairy sent 125 tonnes to South Africa for recycling.
Natpak’s cleaning solvents waste used requires ongoing management. The used cleaning solvents are distilled with a recovery in excess of 70% for reuse.
A number of the IAL businesses have moved across to reusing packaging rather than collecting it for recycling. Colcom started selling reusable durable branded Colcom bags at all its Colcom Shops.
Innscor, being a food manufacturer, follows stringent regulations on the type of packaging allowed for packaging food products.
To ensure customer health and safety, all our packaging is currently made from virgin plastic and the key packaging supplier within the Group, Natpak is compliant to Global Standard (BRCGS) certification for packaging. The standard will be the guiding principle used for increasing the recycled component of packaging going forwards.
Where recycled input material has been used within the Group, this has been for the production of recycled plastic items made by Natpak. Recycled coloured and smoky LDPE plastic waste from the production processes are recycled into pellets which are used internally to produce black sheeting, bin bags and secondary packaging. For external customers the pellets are used to make kitchenware such as plates, dishes and laundry baskets. A total of 831.6 tonnes of plastic was recycled in F2024; an increase of 7% compared to F2023.
Alpha Packaging, the other packaging business within the Group, produces corrugated boxes and egg trays. 100% of waste paper is used to produce egg trays. A total of 873 tonnes of recycled paper was used for egg tray production in F2024.
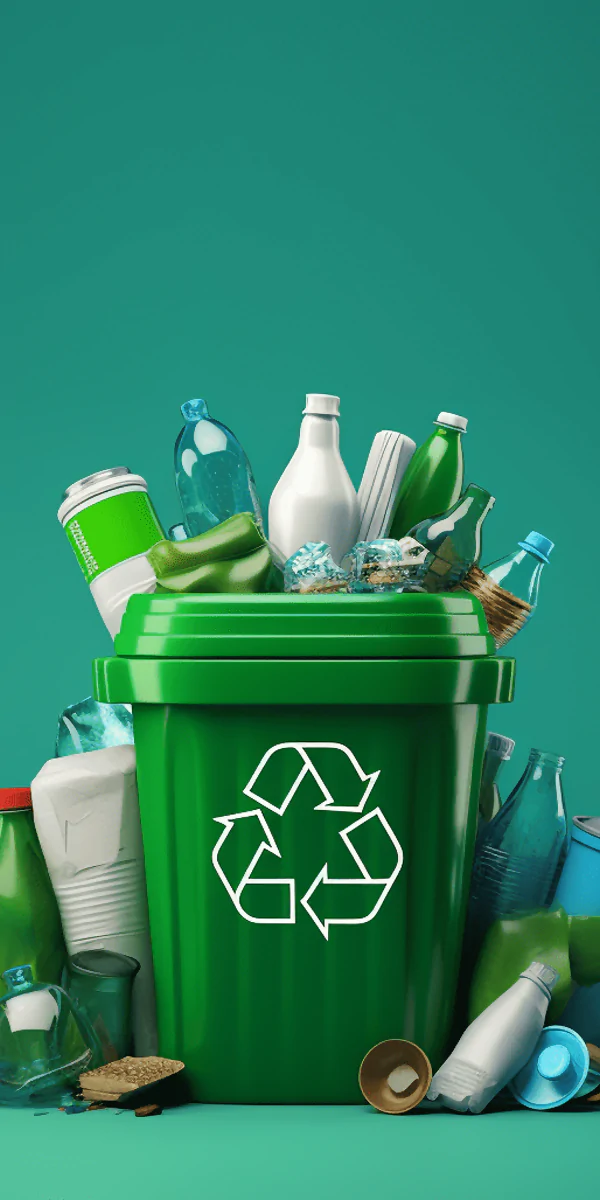
Reduced Packaging
Probottlers is the largest consumer of plastic bottles packaging in the Group and has been focusing on reduced plastic use in F2024. The width and thickness of the labels used has been reduced as well as the individual weight of Probottlers H2GO water bottle. The weight of each bottle has been reduced from 22g to a 16g preform for carbonated soft drinks, reducing the amount of plastic used by 25%. By also reducing the grammage of HDPE used on closures from 2.5g to 2.2g Probottlers reduced usage by 12%.
Sustainable Resource Use
Overview
Efficiency in the use of materials is key to the Group’s objective to reduce our negative environmental impact as well as a driver for profitability. By setting objectives with corresponding targets, each business is working towards optimising the use of natural resources with the aim to improve the efficiency of production processes and systems. The efficient use of resources translates to reduce cost of production as well as reduce negative impacts on the environment.
Management Approach
The Group aspires to align energy management to international standards and best practices, benchmarked against our peers.
We are committed to implementing appropriate climate-related innovations and opportunities thereby enhancing sustainable development practices.
We endeavour to ensure efficient energy utilisation and cost savings throughout our operations. The Group takes active measures to manage energy through energy budgets, which are tracked against actual consumption. Electricity readings, fuel (petrol and diesel) consumption and coal usage recordings are done daily, weekly or monthly. This data provides management with useful information for evaluating performance and corrective action required on energy supply and consumption. Retooling through the implementation of more energy efficient machinery is considered when evaluating the purchase of new machinery.
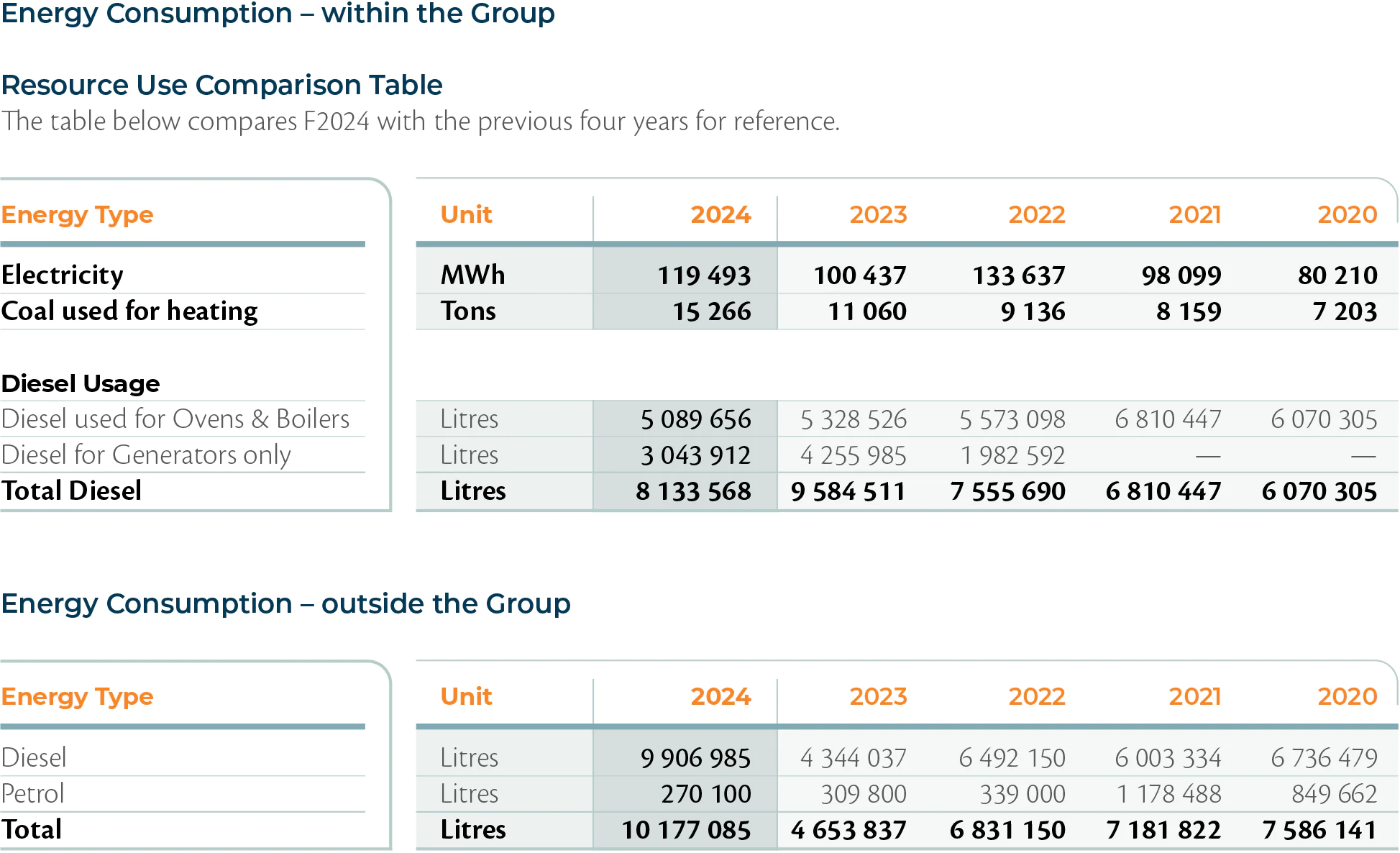
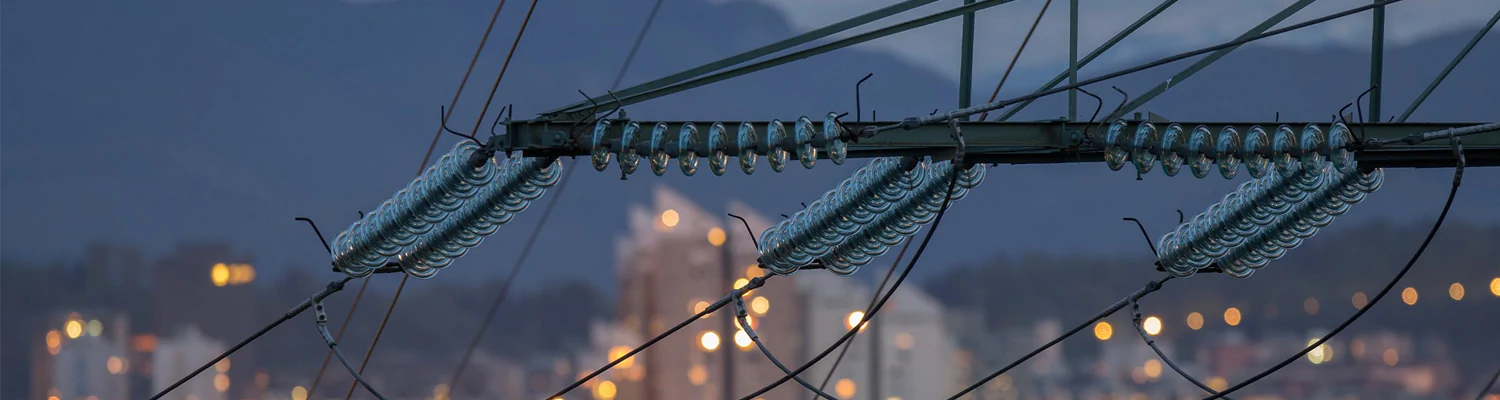
Electricity Usage

The Group used a total of 119 493 MWh. The availability of grid fed electricity improved in F2024 with the Group seeing an 18.97% increase in electricity usage.
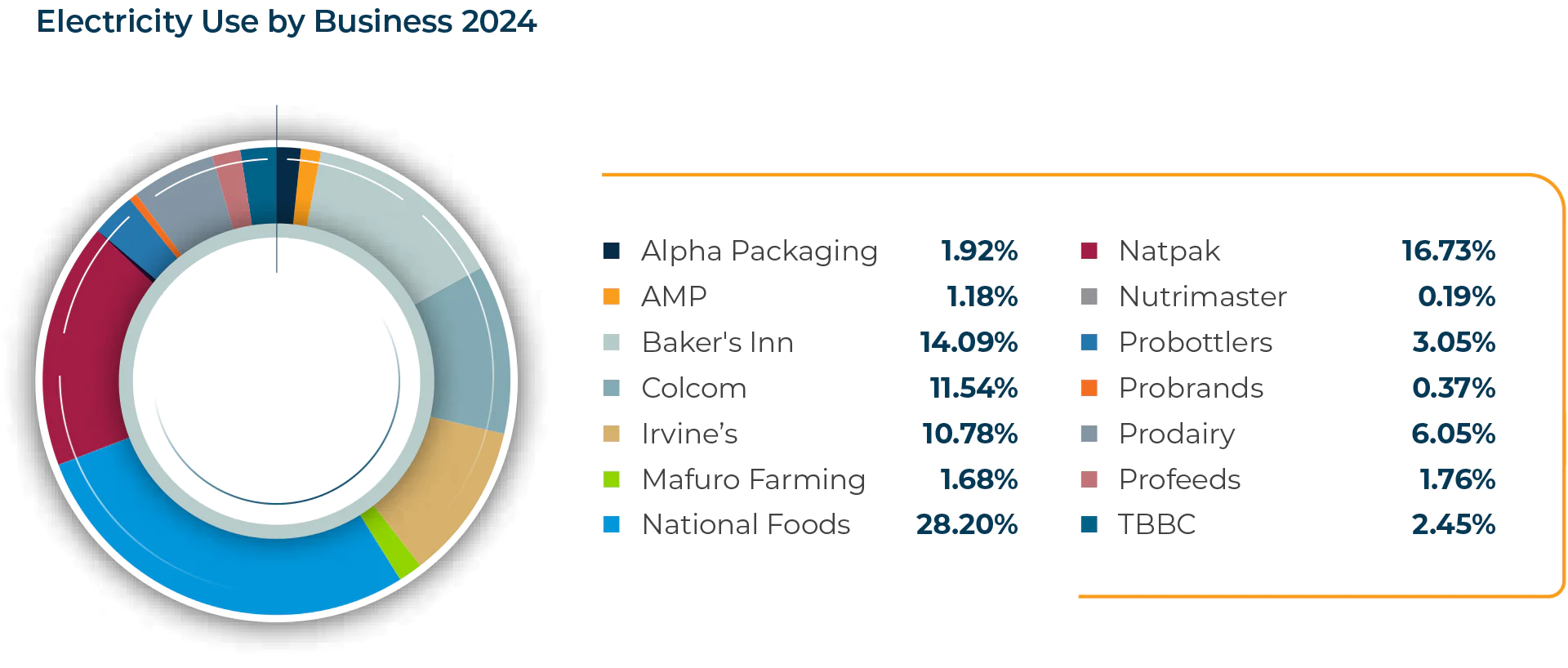
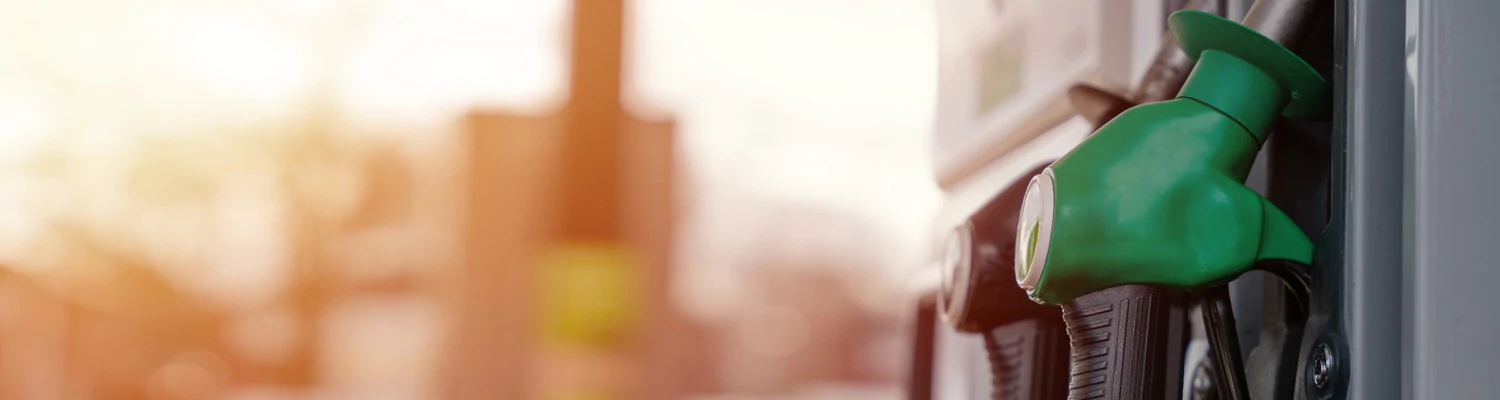
Diesel Usage
A total of 8 133 568 litres of diesel was used by the Group for production (5 089 656 litres) and generator usage (3 043 912 litres) compared to 9 584 511 litres in 2023; a drop of 15%.
This drop in diesel usage is as a result of a 28% drop in diesel to run generators usage as the availability of grid fed electricity improved during F2024.
The businesses are also starting to migrate from diesel run to electric or LPG run forklifts, reducing the amount of diesel for processing needed while improving air quality and efficiency.
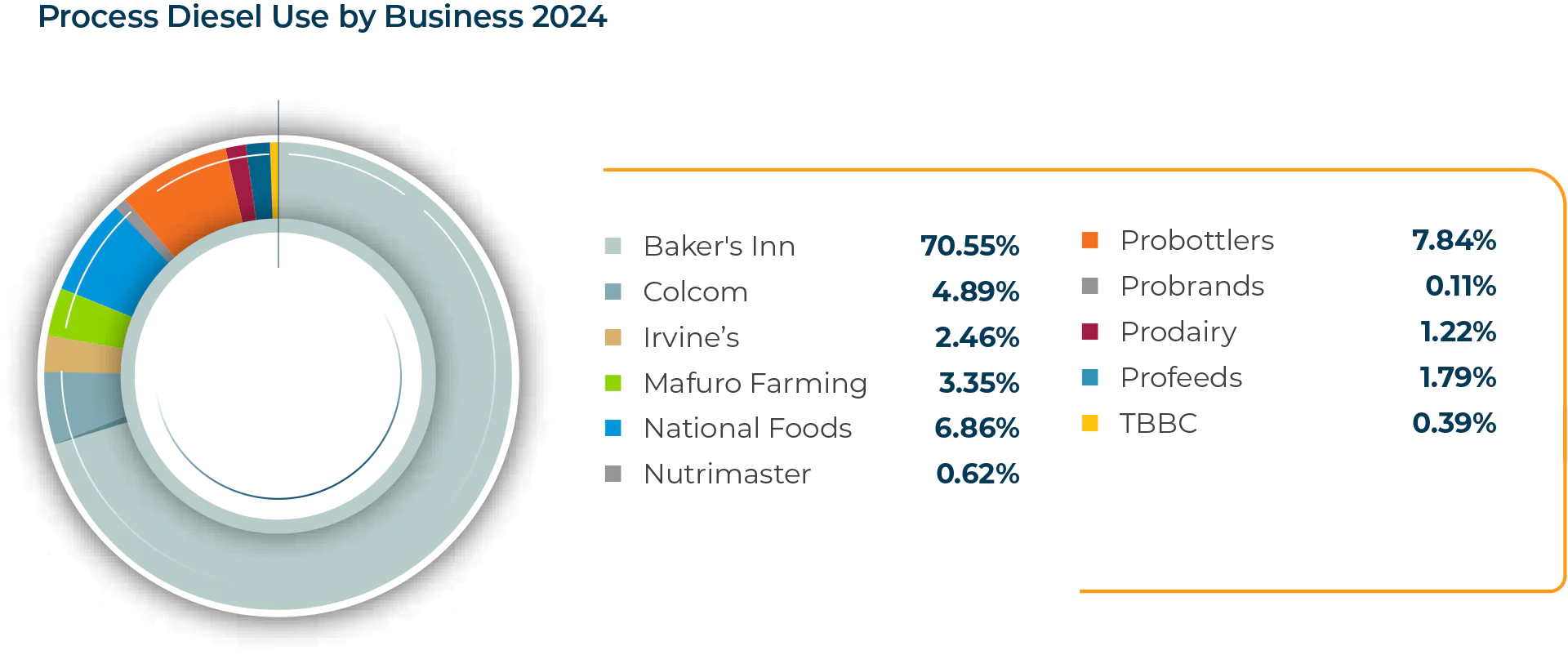
The Innscor Group of businesses recorded 3 043 912 litres of diesel used to run generators as a result of power outages experienced throughout the reporting year; a decrease of 28% compared to F2023.
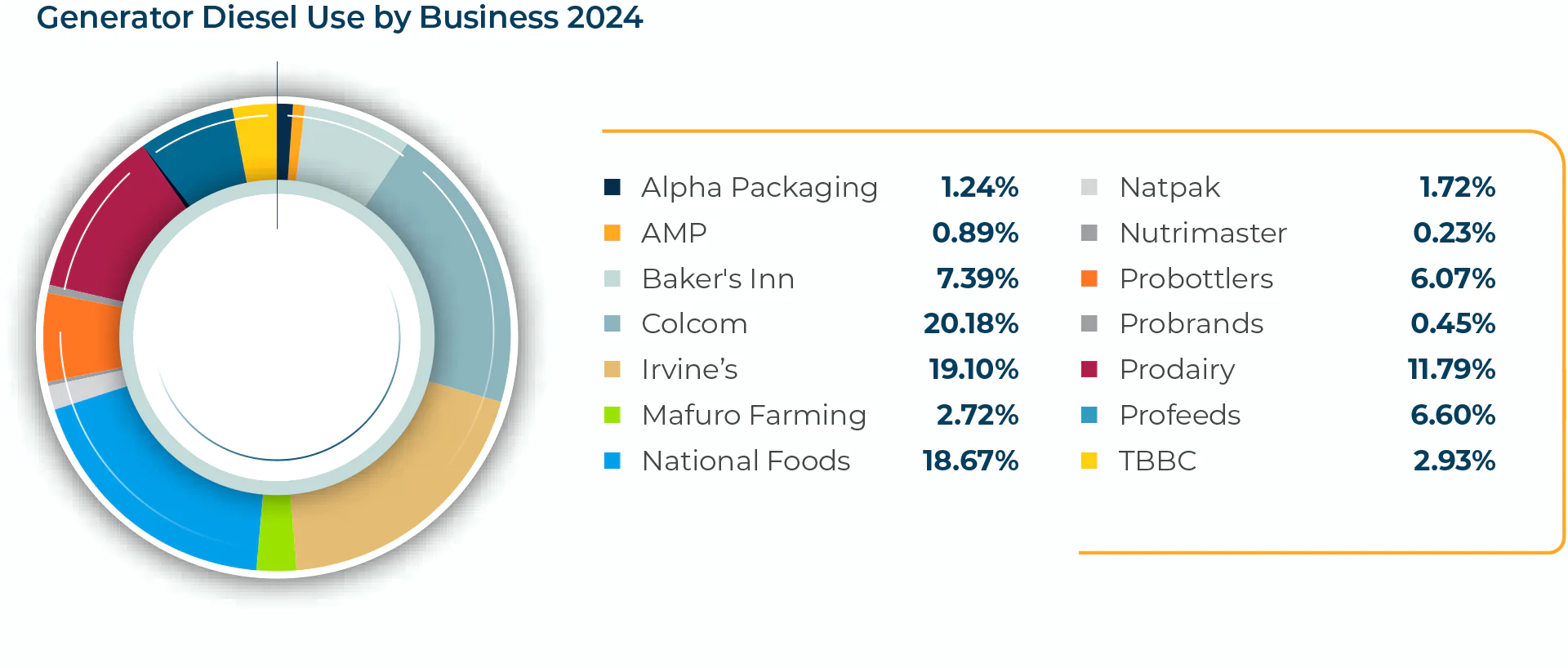
A total of 15 266 tonnes of coal were used by the Group for processing during the reporting year.
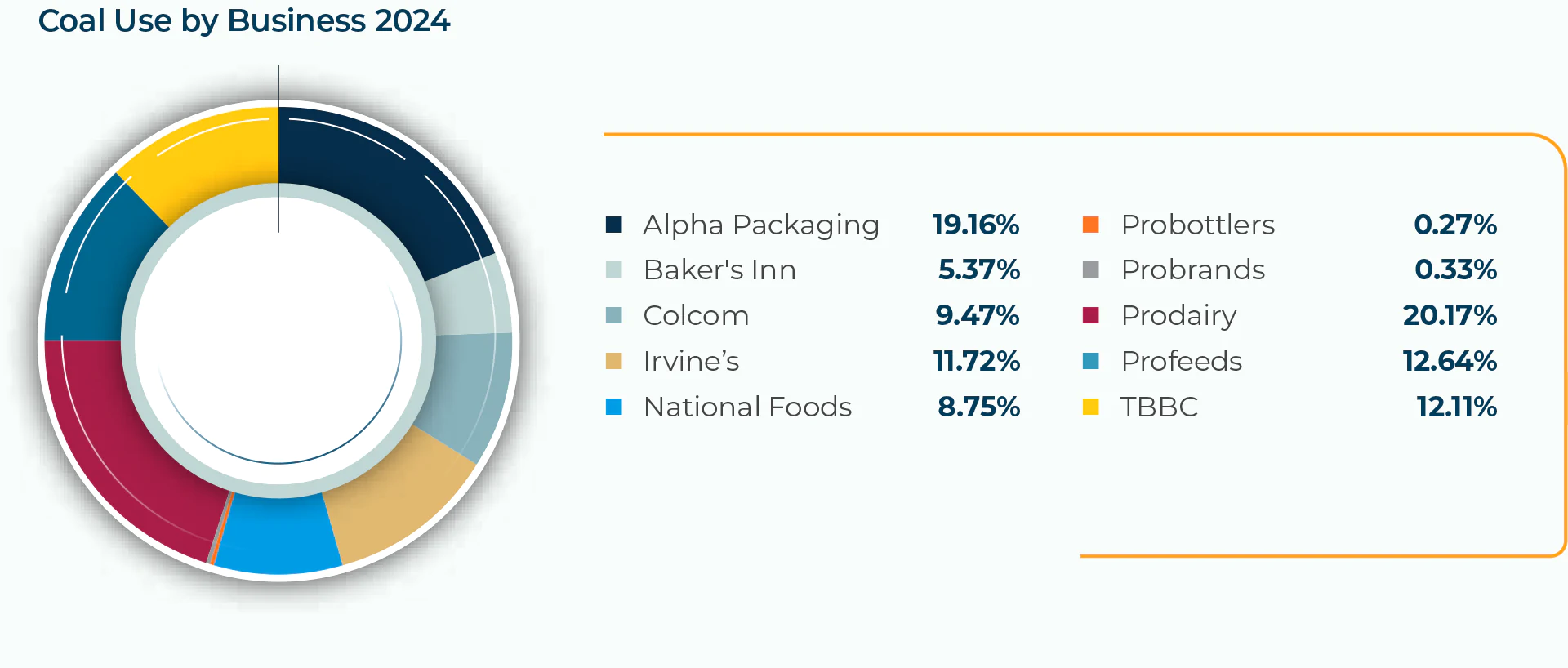
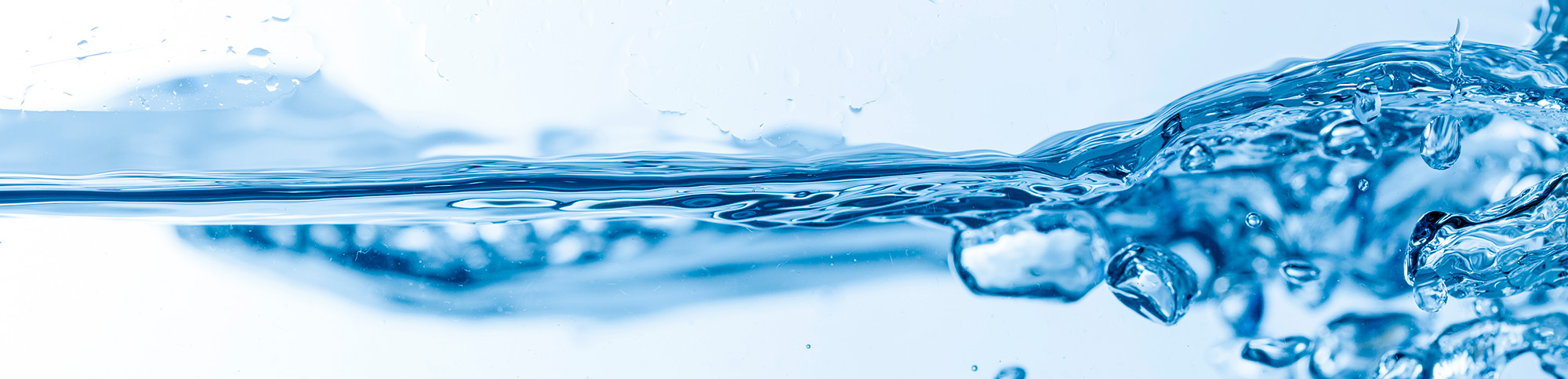
Water Usage
For our production processes, including farming practices, the Group requires large quantities of water. For the manufacturing businesses the water supply is sourced predominantly from boreholes with municipal water and bought-in water providing the balance. The farming operations rely on borehole and dam water.
The Group's policies form the basis for the management of water supply, use and disposal. Going forward improved monitoring and management of water resources is considered high priority.
Actions to manage water and effluent include the following:
- Ongoing compliance with requirements from EMA, ZINWA and local catchment authorities
- Improved awareness on water stewardship and engagement with shared water users
- Implementation of water management plans and water conservation programme, which ties water usage to tonne of product or number of personnel for dry processes
- Borehole capacity and water quality testing
- Meters and automated taps installation
- Effluent metering and quality testing
The Group used a total of 3 365 709m3 of water. 3.18% was sourced from municipal water provided by City Councils and Local Authorities and 45.77% from borehole water with the balance of 51.05% from dams. The Group’s free range pasture dairy, Mafuro Farming, expanded in F2024 to include a new farm outside Kwekwe. As a result of this, the Group’s dam water usage has increased significantly. Mafuro Farming accounted for 44.74% of the Group’s total water usage.
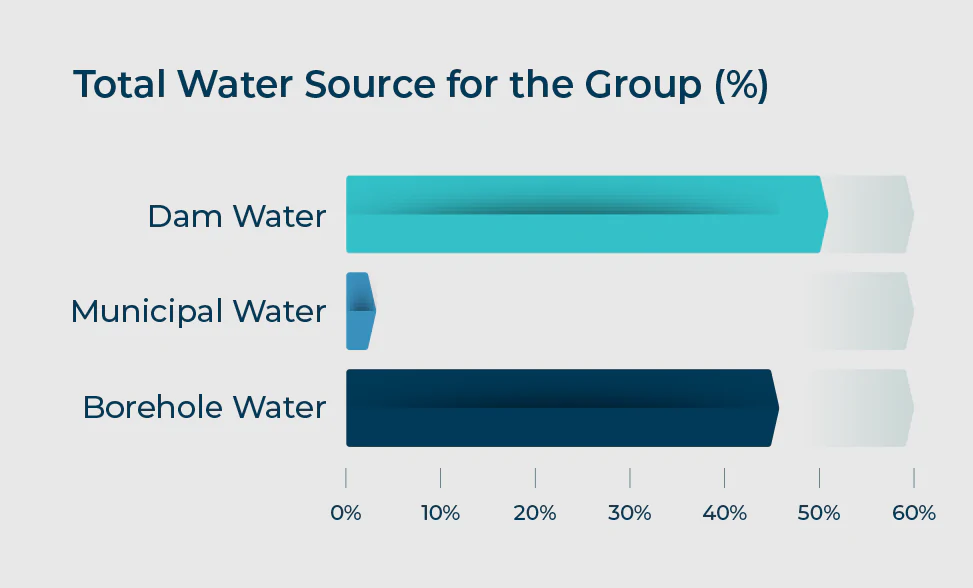
Water Conservation Initiatives
As discussed above, the Group is working towards reducing its water usage rather than water consumption, i.e. the water volume that is used for non-product related purposes such as cleaning or for the ablutions. One key approach to water conservation being implemented across the Group is behavioural change, by making employees aware of the importance of conserving water and by businesses installing water efficient faucets to reduce water usage.
The Group has instigated a number of water conservation initiatives within its operating procedures to further reduce their water usage. AMP Meats, for example, has implemented a leak detection and repair system where, through regular monitoring, leaks can be identified on a daily basis. At Profeeds condensate steam at the boilers points is reused as a water source while Irvine’s recycles 80m3 of water a day for cleaning crates. The Baker’s Inn’s new plant in Bulawayo uses the latest technology for its cooling system and crate washing to minimise water usage. At TBBC through condensate recovery of over 70% and reduced water consumption ration by over 35%, TBBC strives to minimise its water usage footprint.
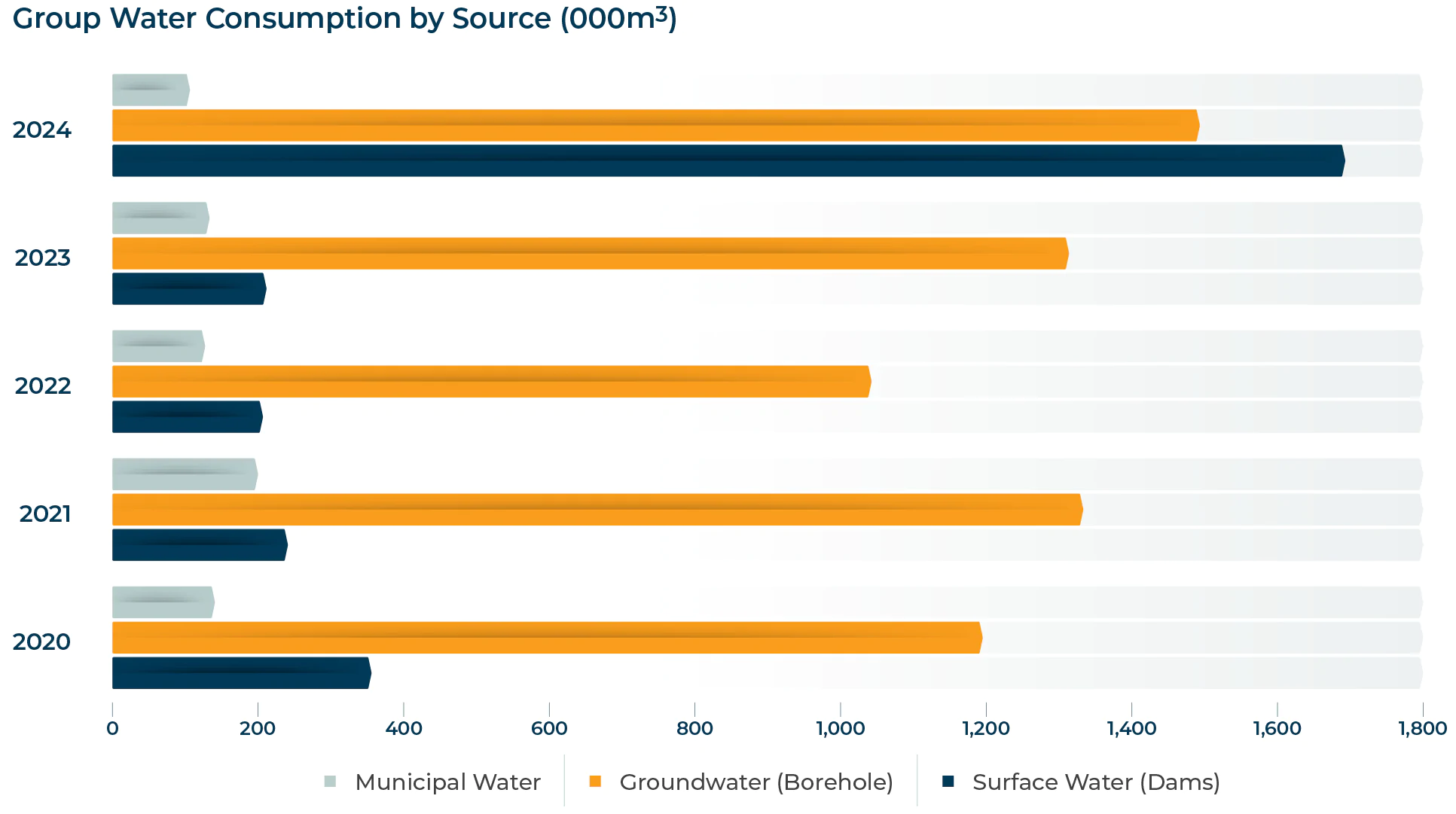
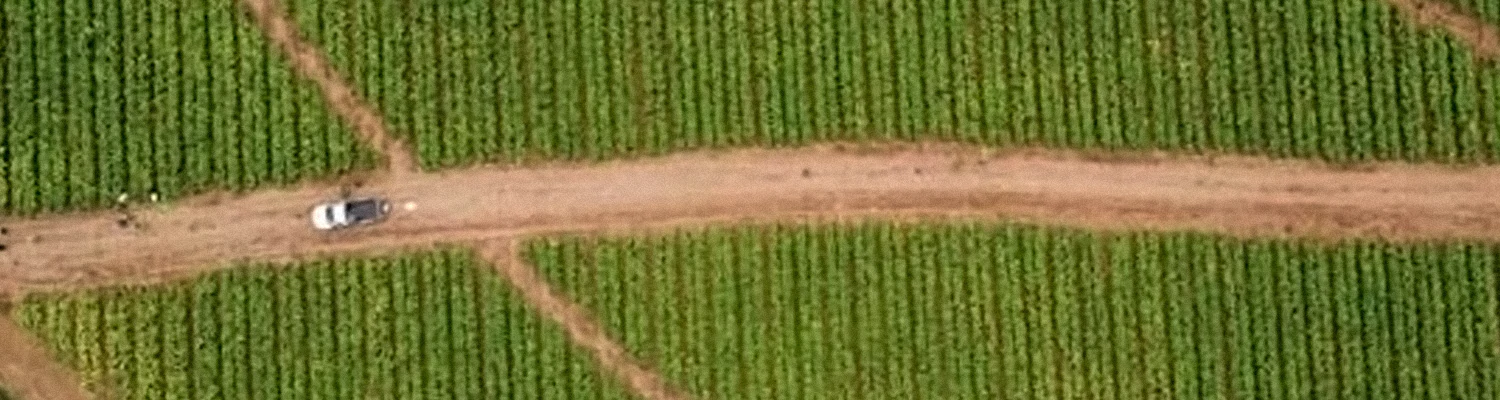
Headlands Farm
Climate Change Mitigation and Adaptation
Overview
The effects of climate change have become a global concern for all businesses. The Group recognises that our operations contribute to climate change in some way and it is therefore the Group’s responsibility to ensure that its businesses respond proactively to calls for climate change protection and mitigation.
Changes in climate can in turn have an impact on our businesses, particularly those that rely heavily on water and on agricultural inputs. Climate change has the potential to significantly impact the Group and is considered a key aspect of business operations and strategy.The Group anticipates that climate related changes affecting its businesses would include changes in weather patterns. The impact of climate change further afield can create uncertainty by affecting the Group’s supply chain requiring that the Group adapts its supply chain strategies in order to mitigate potential disruptions.
Management Approach
The Group recognises the risk of climate change to its operations and is committed to enhancing its response to climate change mitigation and adaptation. In addition, we are conscious of the climate impact associated with our fossil fuel consumption and are committed to ensuring efficient operations
The use of energy is a critical component of the Group’s operations in the manufacture, packaging and distribution of our products. We largely depend on grid electricity, which is supported by diesel powered generators during power cuts. For the transportation of raw materials to our operations and distribution of the final products to our customers, we rely on a fleet of vehicles run by various logistics operations within and outside of the Group. Our fuel consumption therefore extends beyond purely our production processes.
The Group’s management approach is guided by the United Nations Framework Convention on Climate Change (UNFCCC) along with national frameworks such as the National Climate Policy, Climate Response Strategy, and upcoming Climate Change Management Bill. Examples of key risks and opportunities are presented below along with activities that the Group is already implementing.
Regulatory Risks and Opportunities:
- Stricter emissions regulations can impact the Group’s reliance on coal-fired boilers. Non-compliance may lead to fines and penalties. The Group is investing in solar energy to minimise impacts, risk, optimise energy usage and reduce long-term energy expenses. This investment also provides an opportunity for alternative energy sources and reduced reliance on grid electricity.
Physical Risks:
- Extreme weather events such as floods and storms can disrupt operations and damage infrastructure resulting in financial losses. The Group continues to consider innovations related to climate adaptation such as resilient infrastructure and climate-smart agriculture.
- Climate impacts on supply chain can cause disruptions such as drought and crop failures and sourcing of materials thereby significantly impacting on operations. The Group continues to assess and enhance supply chain resilience through additional or alternative sourcing, education and assistance.
- Infrastructure vulnerability relating to critical facilities such as our warehouses and data centres face risks from extreme weather with significant cost implications. The Group is evaluating critical facilities to minimise risk.
The Group is committed to implementing appropriate climate-related innovations and opportunities thereby enhancing sustainable development practices. Appropriate systems to calculate the financial implications relating to climate are underway for implementation and reporting in the coming financial year.
Renewable Energy
The Group is mindful of the impact its processes has on the environment, in particular the amount of energy used. In line with this, the Group is committed to assessing and implementing, where practical, the use of renewable energy over traditional energy sources.
Carbon Footprint
The Group recognises that its operations produce Greenhouse Gas emissions and reports on its carbon footprint across all its businesses. The Group continues to use the Department for Environment, Food and Rural Affairs (DEFRA) (United Kingdom’s) UK Government GHG (Greenhouse Gases) Conversion Factors. The information is presented as tonnes of carbon dioxide equivalent (tonnes CO2e) to indicate the global warming potential (GWP) of GHGs, expressed in terms of the GWP of one unit of carbon dioxide (CO2). The GWPs used in the calculations of CO2e are based on the Intergovernmental Panel on Climate Change (IPCC) Fourth Assessment Report (AR4) over a 100-year period. Electricity carbon footprint factors are taken from those developed using IPCC factors by applying the Zimbabwean electrical grid parameters, including both renewable and non-renewable sources as found on www.carbonfootprint.com/international_electricity_factors.html
When reporting on GHGs, there are three scopes of emission included in the calculations:
Scope 1 Calculations including emissions from direct fuel use – e.g. diesel, coal and petrol
Scope 2 Calculations including emissions from indirect sources – electricity
Scope 3 Calculations including indirect emissions not included in Scope 2, e.g. business travel, shipment of goods.
The Group’s carbon footprint is presented below, calculated for Scope 1 and 2.
Scope 1: Direct Emissions
Scope 1 relates to direct emission arising from business activities within our control and ownership. DEFRA Greenhouse gas reporting: conversion factors 2024 were used for these calculations.
The carbon footprint was calculated based on the fuel used for the production processes only. This includes the use of coal as well as diesel used to run ovens, boilers, forklifts and generators.

* The historical data has also been recalculated using the DEFRA 2024 factors to allow the annual data be comparable with the 2024 data.
Scope 2: Indirect Emissions
Scope 2 relates to the emissions arising from the use of electricity generated by a third party or sources over which a company has no control. The data below, including the historical data, has been calculated based on www.carbonfootprint.com/international_electricity_factors.html IPCC calculation value of 0.396065919kgCO2e/kWh for Zimbabwe.

Carbon Footprint for Scope 1 per Business %
In this year’s report each business’ Scope 1 carbon footprint includes coal and diesel used to run ovens, boilers and generators plus the fuel to run company owned fleet vehicles.
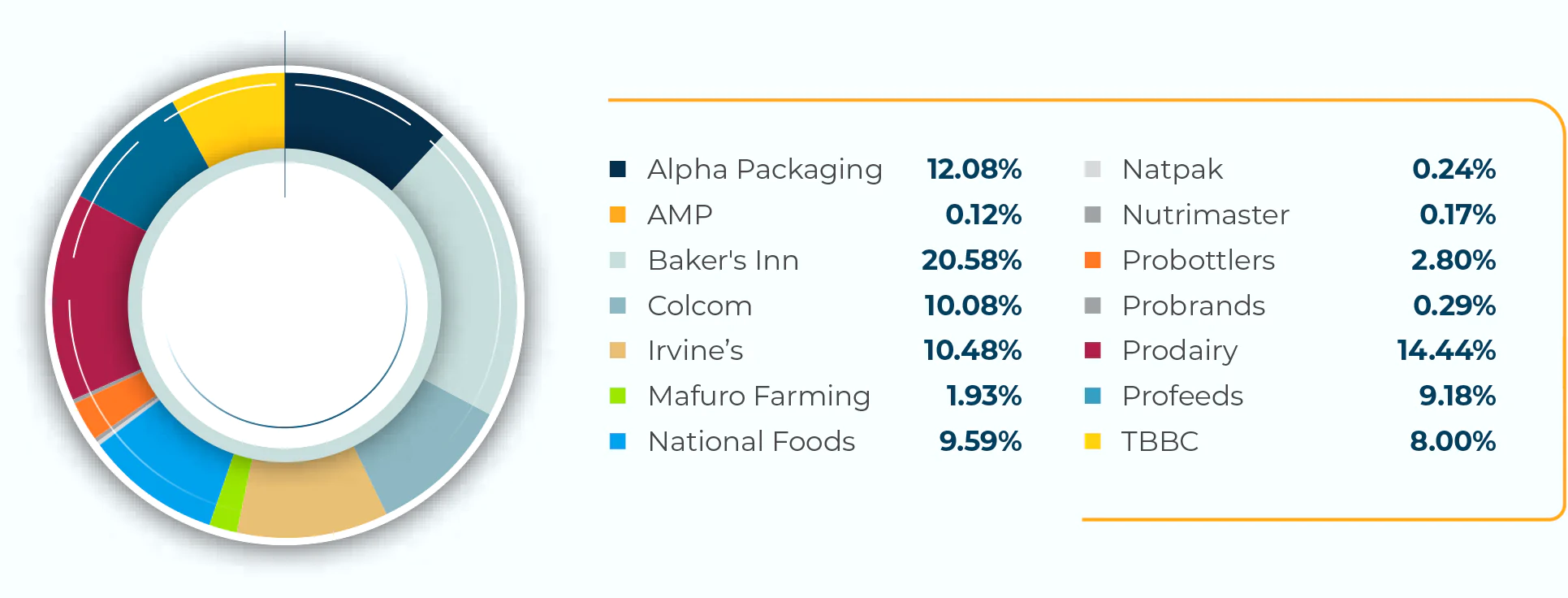
Carbon Footprint for Scope 2 per Business
The Scope 2 carbon footprint focuses purely on emissions from indirect sources which applies to the use of electricity.
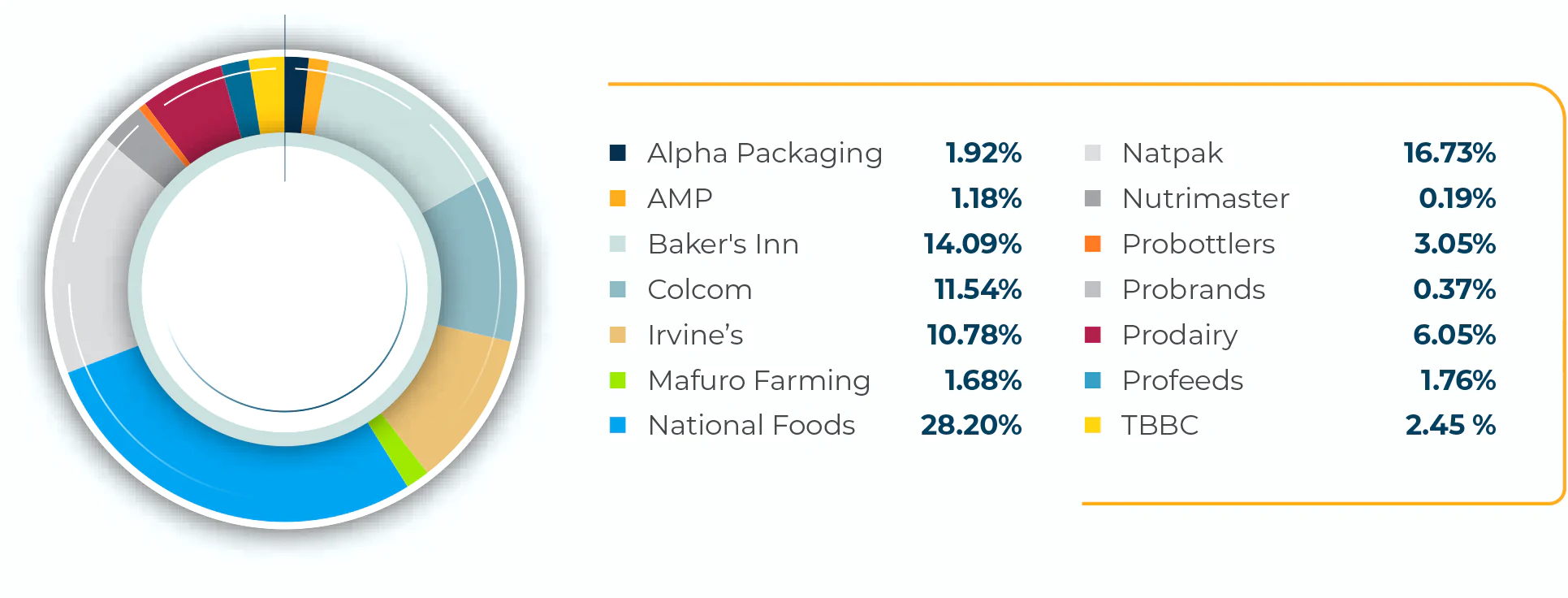